When it comes to space, we often overlook its commercial potential. We tend to focus on rocket launches or the iconic status of astronauts and cosmonauts while widely overlooking what can actually be done in space. The rise of SpaceX, Blue Origin, Rocket Lab, and many others raised a lot of questions about what we could do in space as accessing it suddenly became a whole lot cheaper and not solely exclusive to bureaucratic institutions. This question was recently highlighted to us at Futurama after we read about the renewed interest in Asteroid 16 Psyche after it was estimated to contain $700 quintillion worth of gold. To put that in perspective, that would give every single individual on earth about $93 Billion. Not bad right? But what if I told you there is more potential to space than satellites, astronauts, and the ISS. What if I told you that space could enable us to create things that are simply impossible on earth and force us to rethink manufacturing entirely. Imagine advanced materials that are as light as balsa wood and 7 times stronger than steel, or bio-printed organs that could rid our society of a need for organ transplants. No, we didn’t watch too many science-fiction movies. This is real and it’s just around the corner.
In our newest issue of Futurama, we explore the advent of the space manufacturing industry and dig deep into its history, inflection points, and the underlying science that makes it attractive. We also explore some of the frontrunners in the industry that are leaving a trail of breakthroughs in their tracks.
A Brief History of Space Manufacturing
The roots of in-space manufacturing were seeded in experiments conducted in space decades earlier. Borne from the Cold War, the space race propelled both the US and the Soviet Union to invest heavily in areas of science and technology. The first step into space began with the launch of the Soviet satellite Sputnik into orbit in 1957. By the end of the next decade in an era-defining moment, the landing of the Apollo 11 mission in the Sea of Tranquility in 1969 made Neil Armstrong and Buzz Aldrin the first two humans to walk on the moon.
While landing on the moon was quite a feat, these visits to space were brief. In what would be a frontrunner to the modern-day International Space Station (ISS), the Soviets began constructing a space station. There, scientists could begin to study the effects of a low gravity environment on various living forms and material properties. In 1969, the Soviets conducted the first welding experiment in space during the Soyuz 6 mission. Cosmonauts Valery Kubasaov and Georgy Shonin set up the welding machine, which was pre-programmed to perform three different kinds of welds on various metals and alloys in a depressurized cabin. When they returned to check on the results, they realized that the cabin had been scorched by the welding machine, leading them to flee the room, spending the remainder of their time onboard their craft in a pressurized room.
In 1971, the first space station was launched by the Soviet Union. Salyut (meaning fireworks in Russian), was the first of its kind in a series of 7 space stations designed to operate in low earth orbit (LEO) over the next decade or so. The US responded in kind and launched their own version of a space station in what is known as the Skylab program. Unused equipment from the Apollo missions was repurposed to be used in Skylab. The Skylab was outfitted with a telescope, scientific equipment, a docking port, and solar arrays to power the station. Its features allowed astronauts to conduct spacewalks, perform experiments in different disciplines (such as those relating to biology, life sciences, physics, and material sciences), and make Earth observations.
Common themes in the experiments conducted by both sides were often either biological or physical in nature. Travelers to space were often monitored to better understand the stressors imposed on the human body and psyche by space travel. Cosmonauts or astronauts had to follow a certain diet or exercise plan. Life sciences experiments on plants, bacteria, insects, or small animals were conducted - for example, algae was cultivated onboard Salyut 7 to observe the effects of microgravity on lower plants.
Experiments in physics or manufacturing processes conducted investigated the alloying of metals with different densities, the formation of certain glasses - which would have been impossible without a low gravity environment; crystal growth in the absence of gravity, or the spray coating of metals using an electron beam gun (with possible applications in reconditioning a spacecraft in orbit).
In 1975 the Space Studies Institute, established at Princeton University by Dr. Gerard O’Neill, launched their first conference on space manufacturing, beginning with a discussion on construction, production, psychological impact, and government activities. Over time, the topics grew to cover a broader range including manufacturing, design, construction of space facilities, public policy, and international and legal considerations, with the vision of one day having people live and work in space.
In modern times, the effects of microgravity on biology and physics continue to generate much interest. For example, an experiment was carried out on twin astronauts Scott and Mark Kelly to observe the effects of living in a low gravity environment for an extended period of time on gene expression. Astronaut Scott Kelly spent a year in space, while his brother Mark remained earthbound. What scientists discovered was that the telomeres lengthened while in space (telomeres are a biological marker for aging; they are at maximal length at birth and shorten as we age), and genomic instability increased. Most effects returned to normal within 6 months of returning to Earth, except for a few effects such as chromosomal aberrations (abnormalities in the structure chromosomes, often responsible for genetic disorders) which remained permanent.
With advancements in technology, more companies can begin to conduct their own experiments in a low gravity environment. As shared with us by Yossi Yamin, CEO of Space Pharma and a guest on The Venture Brief Podcast Episode 30, miniaturized laboratories no bigger than a tissue box can be configured to conduct a variety of experiments such as the creation of mononuclear antibodies or to test the properties of fluid physics in the absence of gravity. Freed from gravity, the production of certain items such as optical fibers or organs from stem cells may be more advantageous.
Inflection Points
In every breakthrough technology and emerging market, we believe there to be inflections points at which the solution becomes commercially viable. Just like the improved accuracy of the GPS was a key inflection point in the success of ridesharing services, we have identified which ones will serve the same purpose for in-space manufacturing. Let us walk through them, one by one:
Regulatory Inflection Point: The Privatization of Space
Space, which was once a domain of national interest, entered the realm of private investments with the official signing of the Commercial Space Launch Act of 1984. However, where new frontiers were discovered, commercial interest soon followed.
The first overlap between space and commercial interest began shortly after the successful launch of a satellite by the US. A few weeks before the Communications Satellite Act of 1962 was signed, AT&T launched its own satellite, Telstar 1, with NASA as its launch contractor. The passing of the Communications Satellite Act of 1962 not only allowed communication companies access to satellite technology in the interest of improving their offering, but it also laid the groundwork for a global communications system. Throughout the 60s and 70s, NASA and the US Department of Defense were the sole providers for payload launches in the US. However, NASA could not keep up with the growth in demand for commercial satellite launches, as the shuttle turnaround time was a lot longer than they had anticipated.
Initial interest in providing a private launch service was signaled by the first private rocket launch in 1982. The launch carried out in the Texan plains was not so much a credible competition to NASA; rather, it was meant to show that it was possible. Despite the signing of the Commercial Space Launch Act in 1984, private companies were slow to respond to the deregulation as they perceived it to be commercially difficult to compete with the government-subsidized space shuttle service. This changed in the wake of the Challenger tragedy, where the Reagan administration signed the National Security Decision Directive (NSDD) 254, effectively removing NASA from the market for commercial launches. The NSDD 254 eventually became the amended Commercial Space Launch Act 1988, where the main objective was to promote the growth of the commercial space launch industry. The policy directed NASA to “utilize commercially available goods and services to the fullest extent feasible”, in line with the Reagan administration’s efforts to eschew subsidies and drive the development of the commercial space industry through building a competitive free market for it. Thus, this shift in policy paved way for the beginning of the likes of SpaceX and Blue Origin down the line.
Technological Inflection Points
Accessibility to Space
The price of going to space has decreased drastically over the years as new entrants have challenged the way rockets are built and launched. The average cost of a NASA space launch is about $152M while SpaceX’s launches cost between $62 and $90 million. The cost reduction is better conveyed by looking at the price per kg to get something into orbit. Back in 1981, when NASA sent the space shuttle STS-1 into space, it cost $85,216/kg. In 2020, the Falcon heavy cost $1,411/kg. In roughly 40 years, we have been able to reduce the price by 99% and the cost-cutting continues. In 2019, Musk spoke about launching Starship for $1.5M which would equate to a per kilo price of $10. Even though Musk is known for making bold claims that are often overly optimistic, it is clear that costs are shrinking at a rapid pace.
Obviously, the cheaper a technology gets, the greater the potential for wide-spread usage. But, it is important to understand the forces behind the reduction in cost to get a more nuanced view of what stage the market is in. Below, are some of the key factors behind the sharp decline in the price:
The Reduction in Size of Aircrafts
Naturally, as technologies and machines evolve, they tend to become more compact. Think back to what a phone, computer, or VR set used to look like, and it is clear that time and size are inversely correlated.
The same idea applies to space shuttles and rockets. Even though we are still launching massive rockets into space, we have developed the capability to launch smaller ones that are less costly. In 2018, Japan Aerospace Exploration Agency launched SS-520-5 which was 9.54m tall, 0.52m in diameter, and weighed just 2,600 kgs - just above the average weight of a car.
The smaller the rocket, the more manageable the costs. Astra, one of the startups focused on launching cheap and small satellites into low-earth orbit, is capitalizing on miniaturized space equipment, paving the way for large-scale production of spacecraft. There are many startups gunning for the same mission, and when small-size rockets with a payload size of 165-500 pounds are mass-produced, manufacturing in space will become scalable.
Reusable Launch Systems
Musk stated that if we can figure out how to use rockets like airplanes, the cost of access to space will go down by a factor of a hundred. The SpaceX Starship is being designed as a fully reusable launch system, but we have yet to see these attempts succeed. To successfully get to orbit, the most common launch method used is called “two-stage-to-orbit”. This involves using the first stage to propel the vessel from the ground and up, and then detaching it to return to Earth. This allows the second stage, entering into orbit, to remain light and accelerate easily for the last push into orbit. The issue with fully reusable rocket launches comes down to retrieving both the first and second stages. The first stage has been successfully recovered on various missions, but we are still unable to retrieve and reuse the second stage.
As for the first stage, there are multiple ways of recovering it including retrieving it in the ocean, as seen with Rocket Lab’s Electron, or landing it on a ship, as seen with Falcon 9 for the first time in December 2015.
With Electron, its first stage boosters re-enter the Earth’s atmosphere and are subjected to extreme heat and pressure. Coming in at 2350 m/s and experiencing flow temperatures of 2400 °C, the descent has to be flawless and the equipment built in the most durable way. One of the ways to survive the descent is by using systems that adjust the angle of the descent. This limits the damage caused by the atmosphere when colliding with it. After having re-entered, the parachute system is unveiled to reduce the speed of the booster when hitting the ocean.
As seen in SpaceX’s first stage recovery, the rocket is flipped using thrusters near the top to descend to earth in an upright manner. Shortly after the flip, the boosters reignite to slow the descent, and fins on the side of the rocket are used to steer the rocket to its landing spot. As the landing spot gets closer, the legs are deployed, and the rocket reignites one last time to make for a smooth landing. The rocket’s descent cannot be predicted prior to launch due to unpredictable external factors like wind and air pressure. The rocket has computers on board with dozens of sensors relaying information in real-time to make calculations on the craft’s orientation, position, velocity, acceleration, and altitude, making the landing entirely automated.
So, this is how we currently retrieve the first-stage. However, when we can retrieve everything, making fuel costs the only variable cost, in-space manufacturing will start taking shape in a scalable way. Exactly how second-stage scalable recovery will look like is yet to be seen.
Microfactories have become practical
Microfactories are small-to-medium scale, highly automated manufacturing setups that are easy to move and can operate independently. As machine parts have become smaller, production machinery needed to shrink to be able to produce the components. The concept was first introduced in the 90s but has today been implemented throughout commercial manufacturing processes. There are many significant benefits surrounding microfactories including lower capital cost, lower energy usage, lower operational costs, the flexibility of production, less space needed, etc. As automation advanced, startups began pouring in to the space, increasing the speed of innovation and reducing the size of setups.
For in-space manufacturing to be possible, microfactories have to be well-developed and largely autonomous. They also have to be built specifically for space because of the unique features of microgravity conditions. The use of 3D printing in combination with traditional manufacturing processes has shown great potential.
NASA recently awarded Made In Space with a $73.7M contract to manufacture and assemble spacecraft components in low-earth orbit. The plan is to launch a satellite that will be able to assemble its own power system in space - something that has never been done before. The reason satellite power systems remain so small and inefficient is because the launch exerts such great forces on the spacecraft - which makes launching something that is too big impossible. However, if Made In Space can demonstrate that we can manufacture and assemble power systems while in space, a lot of possibilities open up.
Behavioral Inflection Point: Public Support for Space Exploration
Elon Musk and SpaceX have increased both the public awareness of space exploration but also shown that it is possible for private companies to succeed in the industry. As awareness grows, the number of companies springing up increases in parallel with a fresh influx of capital. The positive flywheel begins as competition, capital, and public support are concocted. Up until 2015, there had not been much investment in the industry, but that year marked a turning point. In 2015 alone, VC firms invested $1.8 billion in private spaceflight companies, more than they had in the previous 15 years. In 2019, VC poured in $5.8 billion in 178 private spaceflight companies. Investments are on an exponential curve and innovation follows along.
Retrieval of Extraterrestial Goods
Another aspect that needs to be in place for in-space manufacturing to be a reality is a retrieval system for space-made goods to return to Earth. Of course, retrieval can also be seen as a flip side of the coin for a launch - after all, to retrieve something from space, one may have to take a journey to space first (although this may not always be the case, as we will see below). However, most companies in the space transport industry are often focused on launches. With a growing interest in-space manufacturing and other space-related activities, however, it is becoming clear that a retrieval system is needed to bring us these extraterrestrial goods.
The current options for retrieval fall into three general categories:
Drones
Examples: X-37B by Boeing, Universal Re-entry Vehicle by Intuitive Machines, Space Rider by Thales Alenia Space Italy, and Avio (in development, scheduled for maiden launch in 2023).
These drones can return to Earth with payloads or travel to another part of space to collect more payload to be delivered back to Earth, making retrieval potentially more efficient and cheaper by collecting nearby goods.
Re-entry Capsules
Examples: Cargo Dragon by SpaceX, Argo by Reusable Transport Space Systems Argo (in development), Spaceworks enterprises Re-Entry Device (RED), JAXA’s HTV re-entry capsule.
Re-entry capsules could perform a docking and undocking maneuver autonomously for arrival and departure at the destination (Cargo Dragon is one such example), be loaded with extraterrestrial goods, and return to Earth. The landing destination for a re-entry capsule is commonly into an ocean near the launch site (known as the “splash site”), making it easy to retrieve the goods safely.
Entire Mini-Factory Returning to Earth
In a special case such as the ST-42 designed by SpaceTango, the free-flying capsule houses both the equipment and the raw materials, meaning the entire capsule will be brought back down to Earth, where the output can be retrieved (cite).
In the near future, we could perhaps expect to see more mini-drones developed for the purpose of collecting smaller payloads, more mini re-entry capsules, or even perhaps - a space elevator? Obayashi, a Japanese construction conglomerate, has plans to develop an elevator to space by 2050.
The Science behind Space Manufacturing
As we have seen in the previous section, access to space is becoming increasingly available at a much lower cost. While we are all aware of this, what is often overlooked is how space access is an enabling factor in working with processes and physical conditions that are either unavailable or too expensive on earth. Nevertheless, the idea of manufacturing goods in orbit or deep space is not as nascent as you might think. Ever since scientists have started to unravel and comprehend the properties of life in space, they have imagined how they could apply these properties in the manufacturing processes of different products. As far back as the end of the 1960s, NASA and other research institutions have been conducting experiments in highlighting how various manufacturing processes can be carried out with greater ease and efficiency in the absence of atmospheric and gravitational disturbances on earth. These experiments led to promising early research and products such as truly spherical ball bearings, high-purity crystals for pharmaceutical purposes, castings of complex objects, vaccines, high-strength materials, etc. Before we dig deeper into what can be made in space, let's unpack these distinct properties that make manufacturing in space attractive.
One of the most common misconceptions that we have about space is that zero gravity, the state or condition of weightlessness, is a result of no gravity. On the contrary, zero gravity is actually the state in which the net or an apparent effect of the gravitational force is zero. As such, we first need to recognize the key drivers that underlie that effect. To switch our thinking here, imagine throwing a UFO-shaped frisbee (pun intended) into space with no obstacles in your way. The harder you throw the frisbee, the further it will fall away from you, and the greater the curvature of its trajectory. You might even throw your frisbee so hard that it reaches a velocity so high that the curvature of the frisbee transitions into a closed circle, placing it in orbit. Although the frisbee is continuously pulled towards the ground as a result of gravity, the frisbee will never meet the ground as it falls away from it at a rate equal to the force pulling it in the direction of the curvature of the trajectory.
That is why maintaining a spacecraft in orbit around the earth is more a matter of horizontal speed rather than altitude. That is why the launch of a spacecraft is not continuously vertical but rather, it follows an outwardly spiral path. This is commonly referred to throughout launches as the roll program. It enables the rocket to reach a certain altitude while achieving and maintaining the velocity needed to reach a stable orbital path. The velocity required to reach orbit is also dependent on the mass of the celestial body. In Earth's case, it is 7,8km/s or about 28,000km/h. Another challenge that ties into achieving the necessary velocity required to reach orbit is the atmosphere itself. At lower altitudes, the atmosphere is so dense that it imposes a drag that can cause the rocket to lose forward momentum.
Once the spacecraft reaches orbit, its contents will also travel at the same velocity as the vehicle itself. Although gravity is still operating in orbit, as long as both the frame of reference and the objects inside it are traveling at the same velocity there will be no relative motion. This creates the perception of the condition of weightlessness, making it appear that the contents of the orbital vehicle are not in a gravity field. The latter perception has been formulated by Albert Einstein in the Principle of Equivalence as part of his Theory of General Relativity.
...we shall therefore assume the complete physical equivalence of a gravitational field and a corresponding acceleration of the reference system.
Einstein’s gravitational field by Peter M. Brown
In his theory, Einstein explains how the internal behavior of a system in free fall as a result of high velocity is equivalent to that of a system that is far removed from a gravity field. Therefore, a zero-g environment is an ‘ideal’ condition that can never truly be achieved in orbit because there exists a number of kinetic effects that create artificial gravity-like forces. Now that we know how gravity operates in orbit, let's dive into how it affects the behavior of physical substances.
Constraints to Physical Substances on Earth
While matter in a solid state can be torn apart while enduring forces much stronger than the acceleration of gravity, the properties of the matter of which it is composed will not change. This is a result of the strength of the composition between atoms and molecules, which allows it to endure a physical force that is many times the force of gravity. For example, matter existing in a solid state such as ice, will retain its shape and rigidity even if broken down to smaller pieces, despite being subjected to such strong forces.
However, matter in a liquid state is profoundly affected by gravity. In a liquid state, due to the intrinsic properties of cohesion and surface tension; the tendency of liquid surfaces to shrink into the minimum surface area possible is of the same order of magnitude as gravity. This behavior of fluid-state matter enables phenomena such as hydrostatic pressure, buoyancy, and gravity-induced convection on earth. Beyond that, some phenomena, which are masked by gravity on earth and often used in several manufacturing processes, are more effective in a zero-g environment. In order to understand the benefits of in-space manufacturing, we need to understand the effect of these phenomena on fluid state matter and production processes on earth.
To begin, when an object is submerged in a fluid on earth, its position in the fluid is subject to the buoyancy force defined by the product of its volume, the acceleration of gravity, and the difference in density between the particle and the fluid. This force determines whether the object will rise, remain in suspension or sink depending on the sign of the difference in density. So, if the density of an object is greater than that of the fluid, it will sink, if not, it will rise, and if it is the same it will remain suspended in the position it was first placed.
Hydrostatic pressure forces a fluid to deform under its own weight and triggers the mechanism of a gravity-induced convection. Convection is the result of differences in density brought about by differential heating within a fluid. To illustrate, when water boils, the water at the bottom of the pot is warmer and starts to expand. This makes it less dense and therefore lighter. The colder column of water above, being denser and therefore heavier, is driven by gravity to displace the lighter water. On reaching the bottom of the pot, it too can be warmed up. Once away from the heat source, the warmer water cools, becomes denser and sinks. This cycle of water moving up and down inside the pot will be maintained until either the source of heat is removed or all of the liquid has evaporated.
Manufacturing Efficiency in Orbit
The motion of fluids, as a result of such phenomena, impedes the quality of solidification, the process of cooling down matter from a fluid to a solid state in manufacturing processes. As a result of this motion, nucleation occurs which leads to dislocations, an irregularity within a crystal structure that strongly influences and may impair many of the properties of the end product. In manufacturing processes that require the control of crystallization, which is the solidification of atoms or molecules into a highly structured form, nucleation poses a great challenge. These phenomena, while they constrain manufacturing processes on earth, cease to exist in a microgravity environment, opening up a wide array of opportunities. In a microgravity environment, fluid state matter is only subject to surface tension and density is no longer the dominant characteristic of the material. As a result, fluids in orbit form a sphere as it minimizes the surface tension.
While some phenomena that constrain manufacturing processes on Earth cease to exist in orbit, other phenomena that benefit manufacturing processes become more effective. The most relevant phenomenon which is amplified in a microgravity environment is the Marangoni effect. The Marangoni effect, named after Carlo Marangoni, highlights convective flows that are driven by gradients in surface tension, a property of a liquid that causes the surface portion of a liquid to be attracted to another surface. In essence, it indicates that fluid will want to flow from areas of lower surface tension to the region of higher surface tension as that pulls more strongly on the surrounding fluids.
This phenomenon is useful and applied in the production of several high-value goods such as microchips. During the wet phase of the microchip manufacturing process, silicon wagers are lifted out of a bath. During this process, not all the liquid flows back in the container with some remaining attached to the wafer, forming meniscuses. To remove these, air mixed with an organic compound is blown over the wet surface with the aim of increasing the surface tension of the meniscuses so that they can draw more water towards them and form droplets of liquid. Upon becoming too heavy, the droplets fall off, leaving a dry surface. Similar processes would be more effective in microgravity.
Although we have focused on phenomena related to microgravity, there are other benefits to in-space manufacturing that do not involve the state of weightlessness. These benefits tie into the aforementioned manufacturing process of microchips which requires a "hard vacuum". While there are other manufacturing processes that require a vacuum, it is by far the most essential with microchips. Its production process is so delicate that it can only work under ultra-vacuum conditions in which any contaminants that can hinder the quality of the end-product is negligible. Following the first usage of ultra-vacuum in space for the production of microchips in the mid-1990s with WSF (Wake Shield Facility), the potential and feasibility of space vacuum were recognized. Contrary to artificial vacuum on earth which is difficult and expensive to achieve and maintain, the capacity for vacuum in orbit is infinite and perpetual. The WSF proved this, creating a vacuum that was 1,000 to 10,000 times emptier than what is possible on Earth. A space vacuum installation would have an infinite pumping capability, allowing for ultraclean surfaces and the creation of ultrapure materials using high-temperature evaporation.
Shifting our Thinking on Manufacturing
Now that we have covered the main properties of space, we can now shift our thinking and explore how we can use these properties to manufacture products that are either too expensive or impossible to produce on Earth. Before we dive into specific products, we want to highlight the revolutionary processing methods that will spur the commercialization of space. When we started out on this research, we initially thought that the set of products that could be produced in space are limited and would be constrained to a niche market. However, once we unraveled the novel processing methods which are attainable in space, we understood the vast potential that is still left to be unlocked for several industries.
Containerless Processing
As you may have guessed, one of the main constraints to producing at higher efficiency and lower cost on earth is gravity itself. Every single production process on earth either requires a container, within which production can occur, or equipment that can artificially counter the pull of gravity. Both are placing a ceiling on production efficiency as they are either highly expensive or impeding the quality of the end-product as a result of nucleation, contamination, and induced strain. Some solutions such as semi-containerless processes or levitation, through an electromagnetic force, exist to increase quality and purity. Nevertheless, they remain both expensive and impractical. In contrast to Earth, the constant state of weightlessness in orbit offers a practical containerless production process that could enable melting and solidification at greater efficiency.
The efficiency is derived from the lack of energy and machinery that is required to perform movements and transition the raw product across the production process. In addition, the complexity and energy required to maintain the raw materials in a state of levitation are non-existent. This production approach could revolutionize nearly all manufacturing processes, enabling lower energy requirements, higher purity, and accuracy.
Super Heating and Cooling
One of the key feats of containerless processing is the ability to melt material at a temperature far above its melting point. On Earth, the temperature at which we could melt a material is constrained to the container in which it is being melted. In orbit, we could melt nearly any material using sun furnaces (gigantic mirrors that focus the sun’s energy). The ability to melt materials at extreme heat, also known as super heating, allows for higher purity, eradicating nucleation sites and maintaining a solid crystalline structure.
While in orbit we can melt material at extreme heat, we can also achieve near-instant solidification of any material as a result of radiation. Using radiation we can enable super cooling, a condition where we can retain a fluid state at a temperature below that of solidification and use it to trigger near-instant solidification. With super cooling, we are able to avoid stresses on the material that are associated with gravity. Furthermore, super cooling enables the creation of larger mono-crystalline objects that are used in solar panels in addition to fine-grained metals which are very stretchable. On Earth, this process is unattainable as the cooling process is affected by nucleation in addition to boundary layer effects, a thin layer that remains on surfaces, between the liquid and the container wall during the thermal change.
Advanced Casting
Because fluid-state matter in microgravity is evenly distributed, new approaches to casting become possible. This enables us to create shapes and forms with an accuracy that cannot be matched on Earth. For example, we can manufacture through adhesion casting which uses capillary forces, the ability of liquids to flow in narrow spaces and spread across a surface without the use of external energy. As a result, we can build up layers of material, whose thickness can be determined with high accuracy, on the interior or exterior of a mold or form without the need for external energy. The ability to use these capillary forces enables us to create products where high precision is required, such as thin wires and membranes without the risk of contamination. While we are able to work with molds, the density-insensitive environment of microgravity also enables us to work with bubbles. While on Earth, air is lighter than water, and its added buoyancy makes it float upward and quickly burst through water droplets. In space, an air bubble remains in the liquid bubble rather than floating to the top because gravity isn’t pulling the liquid down.
It would enable us to build unprecedentedly large bubbles from materials such as glass and different metals as the air surrounding the bubble can be controlled to suit the product. Moreover, as bubbles do not rise to any surface in microgravity, we can more easily determine their distribution and positioning to create foamed materials with customized physical properties. This could facilitate the creation of materials with the same low density of balsa wood and the high temperature and high strength properties of steel.
Breakthrough Opportunities
For some of you, space manufacturing may sound far off. However, several companies, research institutions, and space agencies have done a tremendous amount of work validating the unique opportunities of space manufacturing. In fact, commercial products have already been developed by private companies such as MadeInSpace (good branding right there). They have gone so far that they might be the first company to create a profitable product in space: special fiber-optic cables. Solidification on Earth has some natural constraints which limit the purity and precision of some end products. With fiber-optic glass this becomes apparent. As the molten glass is stretched into fibers as thin as a fishing line and then solidified, crystallization occurs. This disperses some of the light refracting through it, thus weakening the signals. As the natural phenomena that enhance crystallization cease to exist in orbit, we can create fiber-optic glass that could have as little as one-tenth of the signal loss of silica-based counterparts created on Earth. This would lead to fiber-optic cables that could carry more data over long distances in applications such as telecommunications, lasers, and high-speed internet. Although the price of launching 1kg in orbit is currently around $1400, a route to profitability seems feasible for space-enabled fiber-optic cables. Once the ambitions of SpaceX's Starship become a reality, space-enabled fiber-optic cables may just become a global standard much faster than we currently anticipate.
As we have previously depicted, operating in orbit allows us to melt different materials at temperatures that are not possible on Earth. Beyond that, it also allows us to mix different materials more evenly and get to instantaneous solidification, avoiding the stresses associated with gravity. This opens up a wide array of opportunities for the advanced materials market. While metals made from a single element can be useful, they can gain strength, flexibility, or other special features when they incorporate other elements. This is called an alloy. The ability to use extreme temperatures to mix materials that are not able to mix on Earth allows for breakthrough opportunities in several industries. For example, Techshot is aiming to use the ISS to produce magnesium alloys, based on magnesium, zinc, and calcium, for medical implants. At half the weight of titanium alloy, magnesium alloys would match the density and strength of bone while being harmlessly biodegradable in the body. Due to the density-insensitivity of microgravity, materials blend better and are not mixed according to the density. With microgravity, we can create alloys that are a homogenous blend of materials that are too expensive to be produced in large quantities on Earth and are of far greater quality.
Perhaps one of the most exciting short-term opportunities for space manufacturing may lie in the medical field. The idea of applying microgravity to the medical field has been around for a long time but the search for its applications has only picked up significantly over the past 10 years. The implications of microgravity for medical research and medical devices are far-reaching, ranging from the production of personalized medicine to growing cells, organs, human skin, and artificial protein. While some of these opportunities are further out than others, their impact on our future should not be underestimated. For example, growing artificial proteins and understanding how they work has become essential in order to create better treatments and medications. On Earth, growing artificial proteins is limited by gravity. As gravity forces proteins to grow into flat dimensionless blobs, they become much harder to analyze and understand. On the other hand, space-sown proteins can grow 12x larger than on Earth and into more articulate structures, making it easier for researchers to develop new strategies for drug discovery.
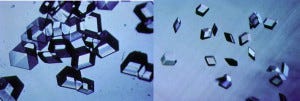
Similar to proteins, the growth of organs, artificial skin, and cells would benefit from the same effects. So much so that it may be possible to grow them profitably in orbit in the coming decade. Existing research on 3D tissue engineering has shown improvements in the size and quality of tissues grown in space compared to those grown on Earth which results in two-dimensional blobs. This was proven by Techshot, which bioprinted a small patch of heart muscle on the ISS, showcasing more uniformity in three dimensions. Further companies and researchers have shown promising early results, growing portions of organs and muscles in microgravity on parabolic and suborbital flights. This would be a game-changer for roughly 120,000 people that are waiting for an organ transplant in the United States alone.
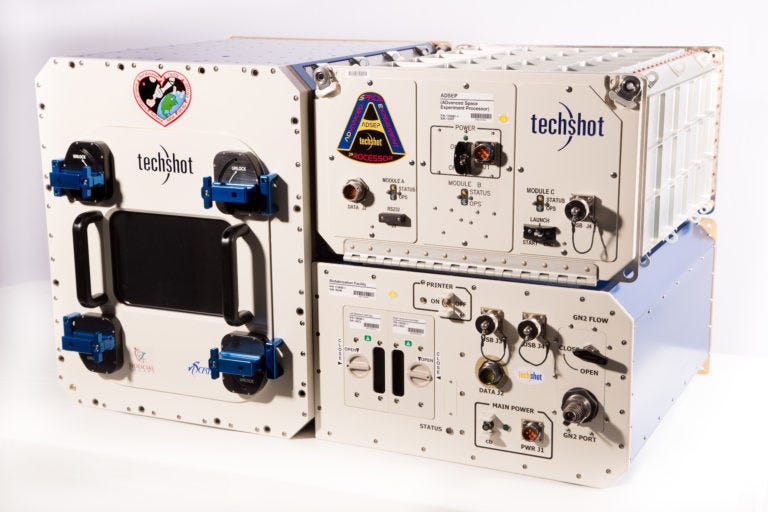
While we could write an entire book solely on what products can be built in space, we decided to focus on these segments as they are inevitable pieces to a future wherein we produce in space. As a result, we have purposefully excluded applications for additive manufacturing and vacuum processing as it relates more to the infrastructure required to allow for space manufacturing as opposed to the actual end-product. If you would like to learn more about other products that could eventually be made in space, take a closer look at Space Factories.
Market Sizing
Although in-space manufacturing is still in its infancy, the items produced in the near future will likely be advanced materials such as optic fibers and perhaps later, biological products. However, since there are no existing factories in space at the moment, we cannot give a prediction of the market size. What we do know, is that the global market size of advanced materials, microprocessors, and fiber-optics amounts to roughly $1770 B. If microgravity lends an extraterrestrial advantage to biological production (such as 3D printing soft tissue using human stem cells in space), or we successfully optimize manufacturing processes in space, we can expect that even more goods will eventually be produced in space. Perhaps far into the future, most high-value fabrication will take place off-world.
Given that in-space manufacturing is not yet a reality, an estimated growth rate is not yet available - however, a general estimated growth rate for the space industry provided by the Bank of America for the next 10 years would be 10.6%. This rate includes other activities such as spacecraft and satellite manufacturing, which is not covered in our market sizing.
Advances in other related areas can serve as a catalyst for in-space manufacturing to take off. Further breakthroughs in material science and biological experiments in LEO research labs, advances in microfactories, launch and retrieval infrastructure, refinement of manufacturing processes in microgravity, and perhaps even in-space construction - building larger factories which can allow for production at scale, can serve as accelerants.
Interest in the space industry has picked up in the last few years. Despite the pandemic, investor sentiments have remained strong, with investments totaling $25.6 B in 2020. With in-space manufacturing being a nascent market, such ambition may take a while to bear fruit. Investor patience is needed, signaled by a shift towards growing reliance on long term capital funds.
Frontrunners
Varda Space Industries
Founding Date: 2020
HQ: California, United States
Founders: Delian Asparouhov, Will Bruey, Daniel Marshall (cite)
Funding Raised: $9M
Stage: Seed
Notable Investors: Founders Fund, Lux Capital
Products manufactured: Undisclosed. Likely to be high-value products such as fiber optics
Introduction
Founded in 2020 by ex-SpaceX engineer Will Bruey(who worked on the Falcon and Dragon crafts (cite) and held the position of Spacecraft Systems Officer of Mission Control with 8 ISS missions under his belt), Daniel Marshall and Delian Asparouhov (Founders Fund) after Asparouhov and Trae Stephans recognized his previous experience in engineering and finance and approached him with the idea of space manufacturing. As of now, there is no announcement on what Varda intends to produce in space, except for a hint that it would be "super high-value and super sensitive materials".
SpacePharma
Founding Date: 2012
HQ: Courgenay, Switzerland
Founders: Yossi Yamin, Martin Aebi
Funding Raised: Undisclosed
Stage: Series A
Notable Investors: State of Mind Ventures
Services offered: End to end service for microgravity services and R&D solutions
Introduction
With the former commander of the Israeli Satellite Unit as one of the founders of Space Pharma, the startup has developed miniaturized labs to scale costs down for experimenting in microgravity. These mini-labs are either fitted to a nanosatellite or installed on board the ISS. In their latest mission involving their nanosatellite DIDO-III, Space Pharma is assisting Italian and Israeli scientists in understanding how microgravity affects the reconfiguration of DNA structures.
Breakthroughs
September 2020: Nanosatellite DIDO-III launched. One of the experiments included are on the effects of microgravity on human aging, which has applications for space travel and space tourism (cite). The launch also provides an opportunity for scientists to test out technological processes that could lay the groundwork for the first trial run of an in-orbit factory (cite).
October 2018: The US National Centre for Advancing Translational Sciences (NCATS) awarded Spacepharma a contract to implement research on using chips implanted in human tissue to counteract muscle wasting by electrical stimulation.
February 2017: Nanosatellite DIDO-II launched, carrying experiments for Spacepharma, Spacety China Ltd, Institute of Mechanics and CAS IPE. The miniaturized lab can perform experiments on different areas of interest such as bacterial growth, antibiotics resistance and particle aggregation dynamics.
Tethers Unlimited
Founding Date: 1994
HQ: Washington, United States
Founders: Robert Hoyt, Robert Forward
Funding Raised: Undisclosed
Stage: Series Unknown
Services offered: Using in-space recycled materials such as metal and plastic to be reused as materials for manufacturing in space, construction, and assembly of large structures in space
Introduction
Tethers Unlimited began in 1994 focused on products and solutions based on space tether technologies, such as space debris cleanup and transportation of people and payload through space. They have since expanded their range to cover space robotic hardware such as the Kraken (a robotic arm that can operate in space) or LEO Knight (a microsatellite capable of repairing and refueling spacecrafts). In addition to an integrated plastic recycler and 3D printer, Tethers Unlimited is also eyeing the space manufacturing/construction area with MakerSat, which is capable of producing carbon beams. If space-built structures can be proven to be structurally sound, this might pave the way in future for large payloads (larger than a rocket) to be constructed in space instead of being hauled up pre-assembled from Earth.
Breakthroughs
January 2020: MakerSat, a manufacturing device that can produce lightweight carbon beams, is being tested by NASA as part of a trial to test space-built structures and the feasibility of manufacturing large structures in space instead of hauling it up pre-assembled from Earth. (cite)
February 2019: Tethers Unlimited’s Refabricator - an integrated plastic recycler and 3D printer was installed on the ISS, which can aid missions in reducing the cost of sending spare tools by 3D printing required tools from plastic waste on demand. (cite)
Space Tango
Founding Date: 2014
HQ: Kentucky, United States
Founders: Twyman Clements, Kris W. Kimel
Funding Raised: $6M (Pitchbook)
Stage: Early stage funding
Products manufactured: In space manufacturing service provider ST-42 (in development) - a capsule that can be launched into LEO containing both equipment and raw materials for in-space manufacturing, a miniaturized lab for experiments in microgravity.
Introduction
Founded in 2014, Space Tango currently offers a miniaturized laboratory for experiments in space and is eyeing to make its first entry into space manufacturing by offering a low gravity manufacturing facility, the ST-42. The ST-42 is a free-flying capsule that can be outfitted with equipment and raw materials for space production. The fully automated ST-42 is intended to remain in orbit for about 30 days before returning to Earth with the equipment and finished goods. The launch is slated for mid 2020s.
Breakthroughs
April 2019: Space Tango launches a commercial payload commissioned by Fiber Optics Manufacturing in Space (FOMS) to evaluate the production of optical fibers in microgravity.
December 2018: In partnership with LamdaVision, Space Tango investigates the manufacturing of protein-based retinal implants, which has applications in age-related vision degeneration.
November 2018: Unveiling of the ST-42, which is intended to function as an in-orbit factory. Equipment and raw materials are loaded up into the capsule, which will spend about 30 days in orbit. Official launch set for the middle of the current decade.
MadeInSpace
Founding Date: 2010
HQ: Florida, United States
Founders: Aaron Kemmer, Jason Dunn, Mike Chen, and Michael Snyder
Funding Raised: Undisclosed
Stage: Acquired
Products manufactured: trialing the manufacturing of optical fibers using a 3D printer and ceramic manufacturing device aboard the ISS
Introduction
After introducing the world’s first 3D printer in space onboard the ISS, MadeInSpace set its sights on bigger challenges, incorporating 3D printing as a core solution. For example, the Archinaut is a set of customizable manufacturing and assembly technologies that can be incorporated into free-flying satellites. Instead of being launched fully assembled, satellites embedded with Archinaut’s technologies can begin to manufacture themselves through 3D printing and self-assembly while in orbit. Their 3D printing efforts also expand to the life sciences sector - through the partnership with Allevi, they aim to explore the creation of biological materials using 3D printing in low gravity environments.
In June 2020, Redwire, a company formed by the merger of two space-related companies - Adcole Space and Deep Space Systems, acquired MadeInSpace for an undisclosed sum.
Breakthroughs
Sept 2020: Ceramic manufacturing module (CMM) sent onboard the ISS.
Oct 2019: MadeInSpace’s first commercially developed plastic recycler is sent onboard the ISS.
Sept 2018: The first phase of MadeInSpace’s attempt to manufacture the first optic fiber cable onboard the ISS. It turns out to be successful and they subsequently plan to enter the second phase by having a larger device onboard.
Jul 2018: MadeInSpace partners with Allevi to experiment with 3D printing of biological materials in microgravity.
Nov 2014: Together with NASA’s Marshall Space Flight Centre, the first 3D printer was remotely operated and the first 3D-printed parts are made in orbit. Their success paves the way for additive manufacturing in space.
2011: First 3D printer that can operate in microgravity developed.
The Future of Space Manufacturing
Today, manufacturing in space only makes sense for products that are impossible to produce on Earth. The value of such products, due to their scarcity and quality, are high enough to justify the cost of manufacturing them in space. Even though it is still economically unfeasible to manufacture products in space that we can still produce on Earth, there will come a time when the value derived from in-space manufacturing outweighs the cost of going to space and back.
Environments that we artificially create on Earth that are complex and high in energy consumption occur naturally in space. The vacuum, the range of temperatures, and the peculiar behavior of matter are important factors in creating a beneficial manufacturing environment, and in space, they are free. Once we start leveraging these factors to create new methods and processes that are tailor-made for in-space manufacturing, we will be well on our way to ramping up production.
We have established that in-space manufacturing is overall much more efficient and effective than manufacturing on Earth. Now, before we see this at scale, the cost of going to space must go down significantly. Elon is working hard on this very issue. He predicts that in 2021, Starship will successfully take to the skies and land. Launch costs will be around $2M, equating to a per kg price of $10 compared to today’s best prices hovering around $1,400/kg. When this happens, the world of in-space manufacturing will become impossible to ignore.
Similar to what Elon did with Starlink, he could do with in-space manufacturing. Starlink was mainly launched to fund SpaceX’s mission of developing rockets that will eventually take people to Mars. By 2040, Morgan Stanley estimates that SpaceX will be worth $100Bn. 90% of this value is attributed to Starlink. With predictions of 364 million subscribers, each paying $21 per month for the satellite broadband service, Starlink will provide SpaceX with an annual recurring revenue stream of $92Bn. Similarly, Starship could be used for in-space manufacturing to fund SpaceX’s main mission of going to Mars. By either leasing out space on the aircraft, or having a monopoly on the in-space produced products, the options are many. Once Starship is successful and more of it is produced, one could imagine SpaceX making an entire Starship into a flying manufacturing facility. However, as monopolies - if profitable - do not tend to last, we will surely see new entrants aiming at in-space manufacturing through focused efforts towards the niche.
One thing is for sure, the costs of going to low-earth orbit are going down and when they are low enough, we will come to a point where it is more cost-efficient to produce goods in space rather than on Earth.
The winners of in-space manufacturing will be the companies that can miniaturize and trim manufacturing environments to create the most out of the least amount of space. This will enable them to load spacecraft with more raw materials rather than wasting payload on heavy manufacturing equipment. The more you can trim the equipment in weight without losing effectiveness or efficiency, the earlier you can reach the break-even point where the costs of going to space are offset by the value produced.
Moreover, the winners will be the ones that tailor their processes and methods to the new conditions in the best way. As we have talked about previously, the phenomena in space can be leveraged to make products of far higher quality than ever possible on Earth. New best practices in manufacturing will begin to take shape as we figure out how to optimize operations under new conditions. The startups that can test rapidly, leave the old ways behind, and use the harsh environment to their advantage are the ones most likely to succeed. Today, we do not know what this looks like, but we know for sure that the age of in-space manufacturing is coming, and with it, stronger and purer products than we have ever seen before.
For too long, we have thought of space as an empty void with a nice view. Now, we must regard it as an extension of Earth’s industry, in which to work and use the conditions present to our advantage. Earth is taking a heavy hit from the waste that we produce in industrial processes and it only makes sense to move that part of our world off-world, to an environment in which we can produce things of better quality while reducing pollution on our planet.
If you enjoyed this issue of Futurama, do share it with one or two curious friends! If you want to stay ahead of the curve and keep an eye on the future, then subscribe above and unlock the future with our monthly Futurama and exclusive podcast episodes straight in your mailbox! If you think we missed anything important or overlooked a mistake in our research, shoot us an email at hello@readfuturama.com.
The future belongs to the curious,
Neal, Lukas, and Shu